Grease in cooling system creates high costs
When grease gets in the cooling system, significant costs come with it. Water treatment, filter changes, and maintenance all add up, not mentioning health and safety issues.
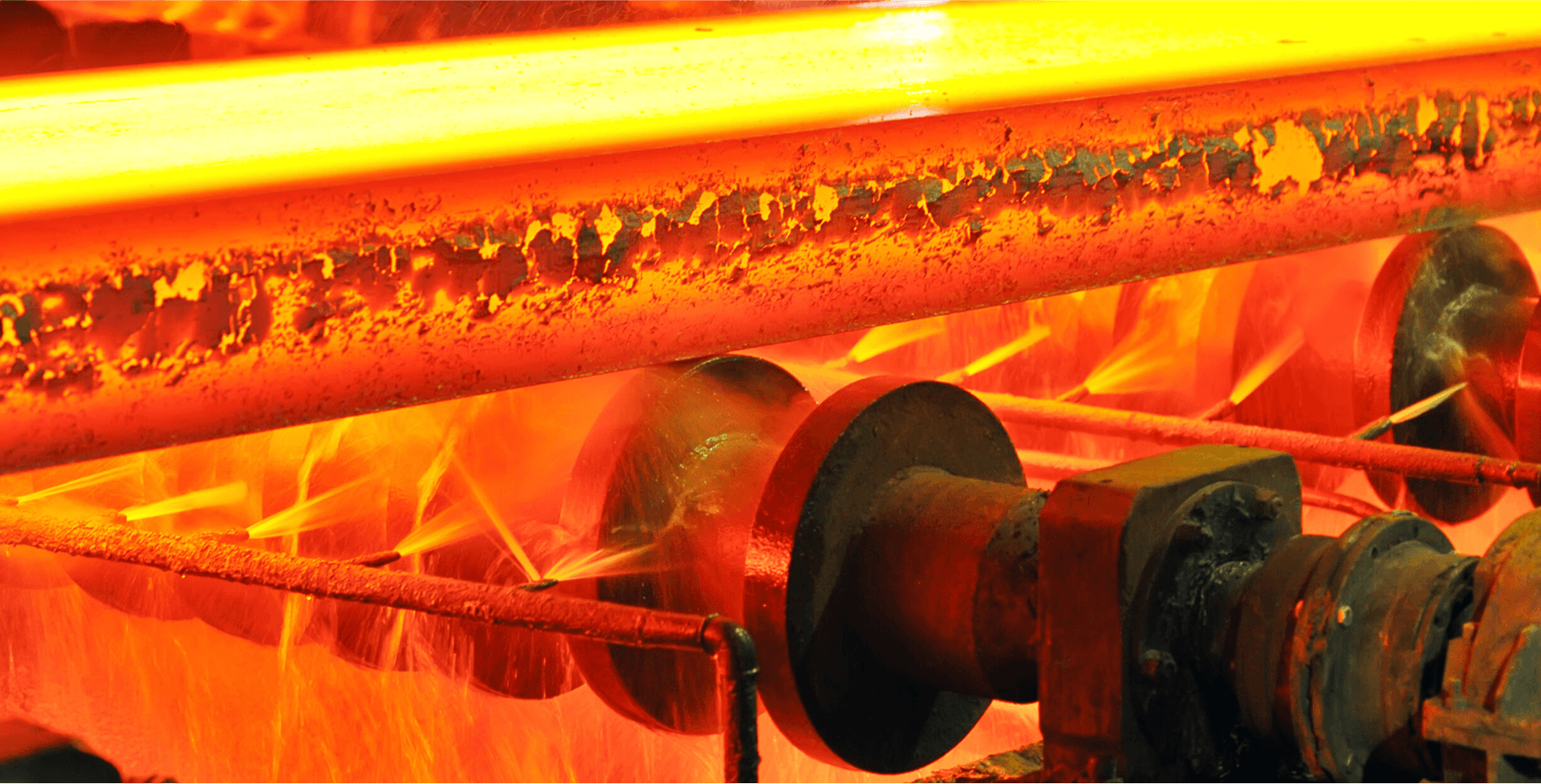
#18
Seals keep lubrication in and contamination out
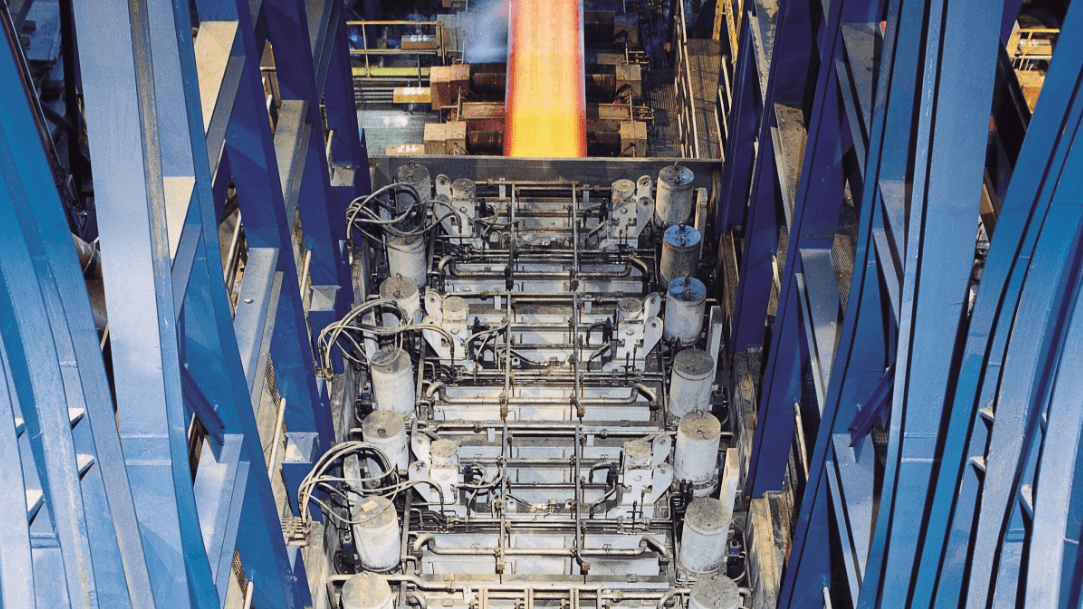
Many of our customers use open bearings in their continuous casters, often out of tradition or habit. However, using open bearings means a risk of contaminations getting into the bearings and lubrication leaking out.
Leaking grease is costly
We often see open bearings leaking grease into the cooling system. This comes with considerable costs for water treatment, filter changes, maintenance, etc. In an example from one of our customers, the purchase price for grease is 4€/kg, but when you add the costs of taking care of grease in the cooling system, the final cost is about 12€/kg.
Sealed bearings stop leaks
With sealed bearings, leaking of grease can be avoided. When you keep grease in the bearing, less of it goes into the cooling system, meaning less fresh water is needed. Recent calculations show that you can save up to 20% on water recycling costs and 20% on freshwater when you use sealed bearings.
Avoid contamination and moisture in the bearing
Seals do not only keep grease inside the bearing. They also keep the bearing free from contamination and moisture, significantly improving bearing performance with less grease demand.