Having the correct availability of spare segments
The availability of spare segments is a common challenge in the metal industry. ArcelorMittal improved this through remanufacturing.
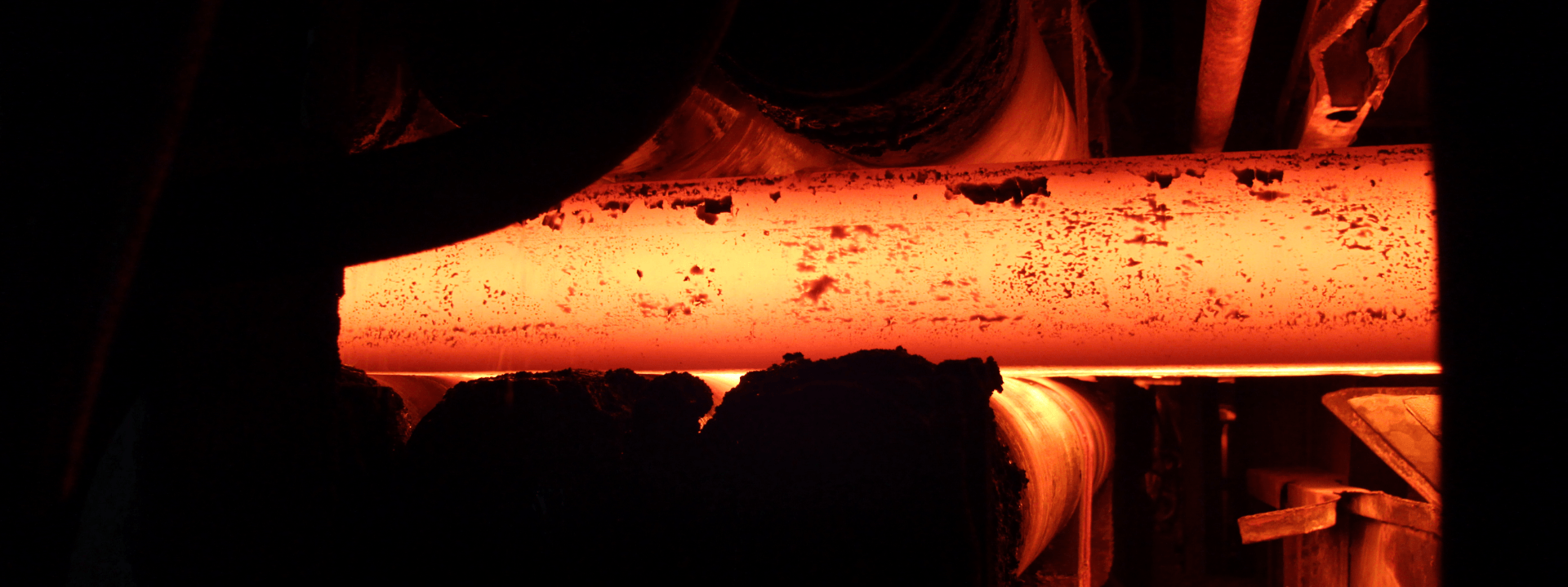
#11
How ArcelorMittal shortens lead times for maintenance of segments
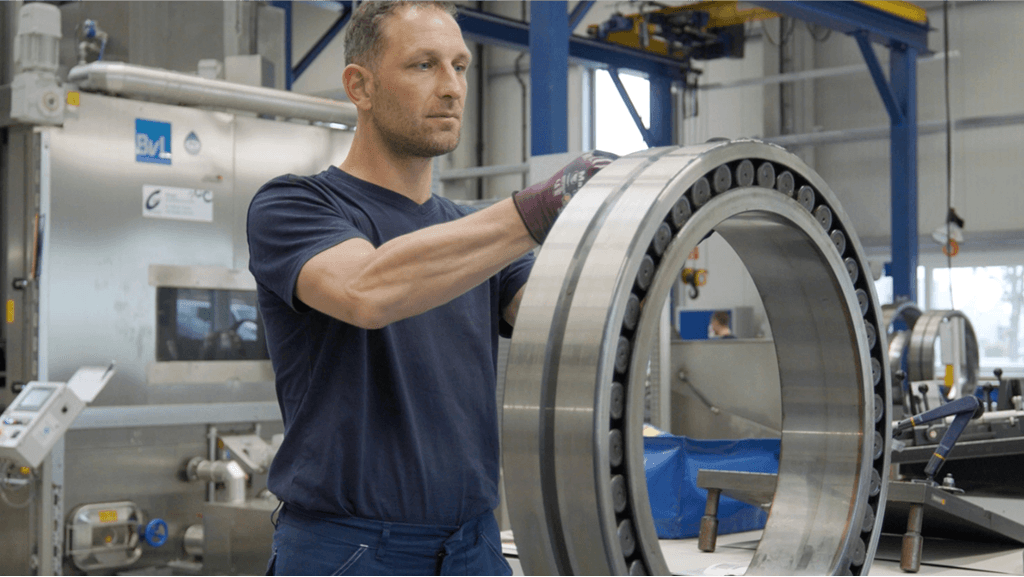
Like many of our metal industry customers, ArcelorMittal constantly seeks new ways to improve productivity and reduce downtime. As a long-term partner, SKF was trusted to supply sealed, relubrication-free roller bearings for a multi-year test of reliability and availability.
After a successful test period, ArcelorMittal signed a five-year performance-based contract with SKF to introduce new technologies in the casting machines of their operations in Fos-sur-Mer, France. In the agreement, SKF not only exchanges spherical and torodial roller bearings from open to sealed bearings but also adds remanufacturing to extend the bearing life cycle.
Better machine availability without building a stock
The bearings will be systematically remanufactured in SKF’s dedicated service centre in Steyr, Austria. Remanufacturing shortens the lead time for the maintenance of segments and combined with a new cladding technology for continuous casting rolls, SKF can significantly prolong the service life of the segments. As a result, ArcelorMittal can achieve improved machine availability without having to stockpile.
At the same time, CO2 emissions are lower from remanufacturing. Depending on the degree of processing, the carbon footprint of a reconditioned bearing can be up to 90% lower compared to manufacturing a new one.
Learn more
In a webinar from SKF, Hannes Leopoldseder, Business Unit Manager at the SKF Industrial Services Centre in Austria, shares some of the learnings SKF has made during two decades of remanufacturing.
- See real-life examples of the results of remanufacturing
- Discover how digitalization improves the outcome of remanufacturing
- Learn how remanufacturing supports the transition to a circular economy
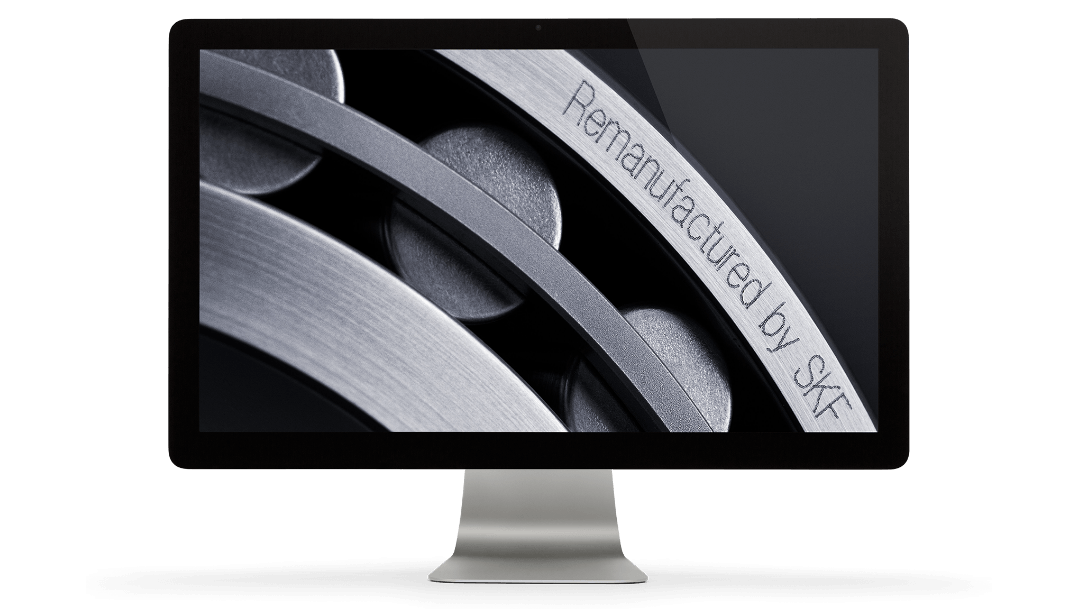