Decarbonisation demands
Legislators put higher and higher demands on the metal industry to decrease CO₂ emissions. SKF helps to meet the demands with remanufacturing – and not only bearings.
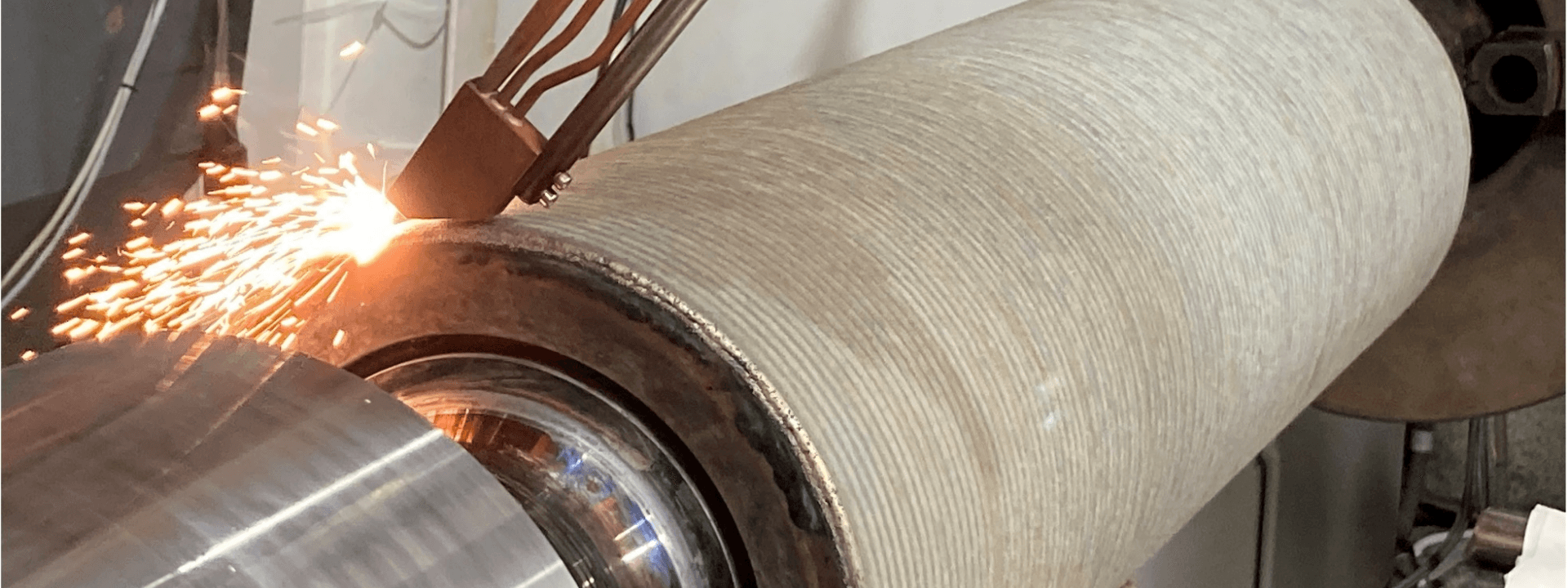
#4
Reduce CO₂ by new methods of remanufacturing
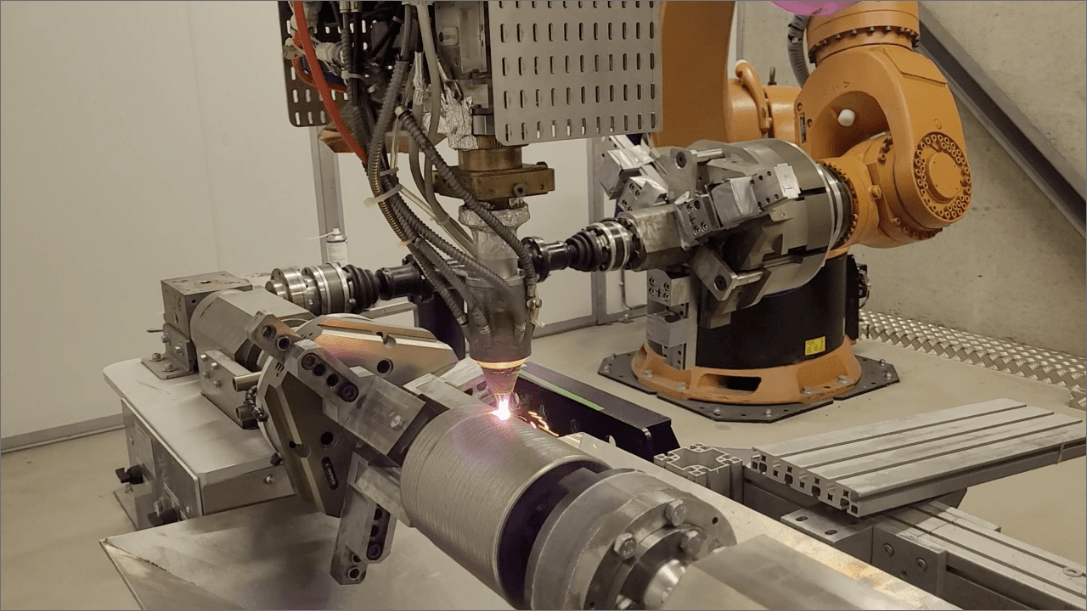
The metal industry is constantly in the spotlight for reducing carbon emissions. To help our customers with that, SKF offers remanufacturing of both bearings and caster rolls. But instead of the traditional welding technology, we use laser cladding.
Adding laser cladding of caster rolls to your remanufacturing routine can increase performance, prolong service life, and reduce your carbon footprint.
Less energy and less CO₂ than welding
Remanufacturing caster rolls with laser cladding uses 90% less energy than conventional welding, and no additional heat treatment is needed afterwards. This means more than 50% less electricity is required, meaning significant cost savings with today ́s energy prices. Up to 70% of CO₂ emissions can be saved.
Stable metal structures
The SKF laser cladding method heats only the outer layer of the caster roll, which then cools off very quickly. This means that the metal structure of the caster roll, except for the part that gets a new layer, is unchanged. It also means that it is possible to add the new layer all the way to the end of the roll.
Better performance
When we add a new layer of metal to your caster roll, we can alter the characteristics of the roll at the same time. With the right chemical composition of the added layer, you can optimize the surface properties related to application requirements.
An example of laser cladding.