Cut cost per ton
Planned and unplanned downtime increases cost per ton. Solutions and services from SKF help customers to reduce both.
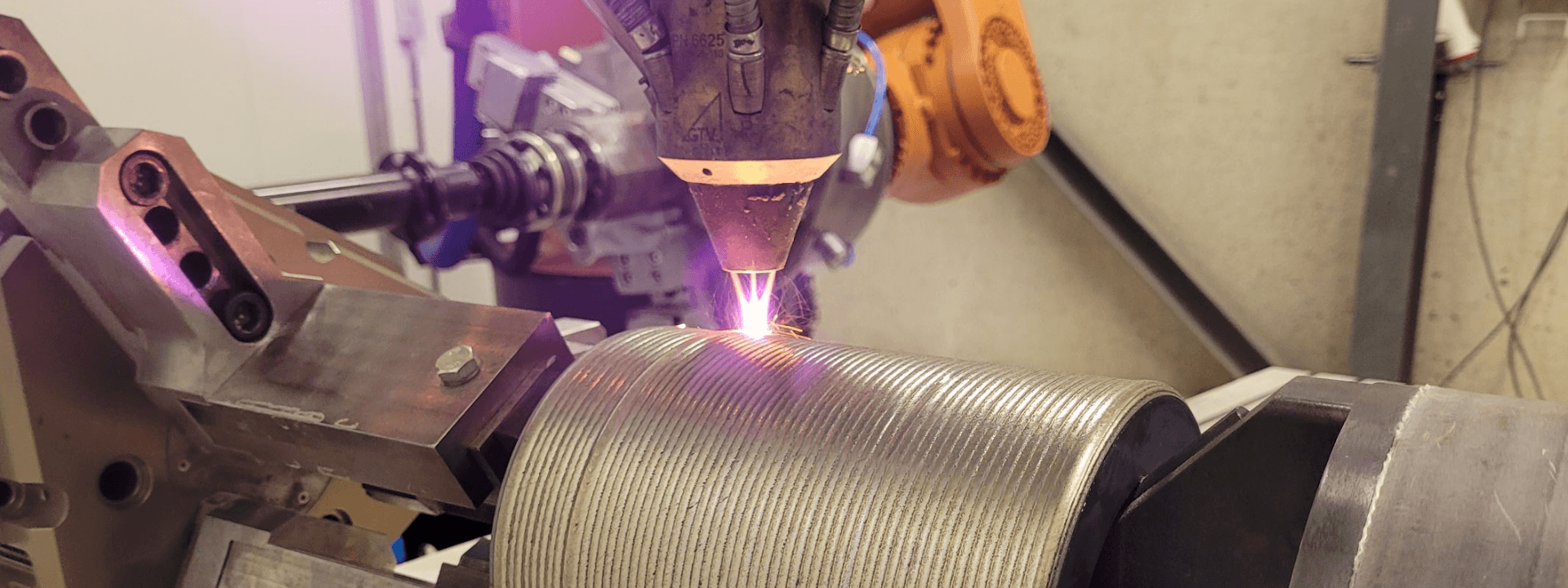
#10
Three ways to keep your machines running
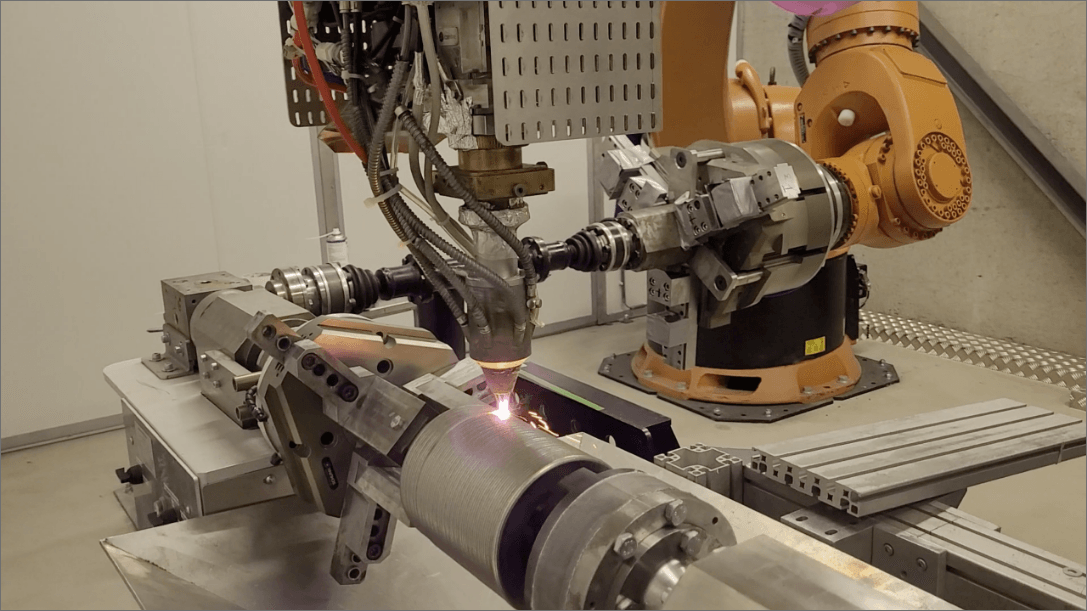
Having both planned and unplanned downtime is a driver that increases costs per ton. To take control of your planned bearing maintenance, a great way to start is to choose bearings with the right service life for your application and add a condition monitoring system. However, there are also ways that SKF solutions can reduce unplanned downtime and support better machine availability.
According to this Forbes article from 2022, there are several ways to cut excessive downtime, and SKF can support you with several of them. These are three ways that SKF solutions can assist you in your efforts to reduce costs:
- Spare part management – making sure that spare parts are always readily available.
- Exchanging open bearings for sealed bearings – less grease is needed and less grease is washed out into the cooling system,. This means there is no need for water treatment for cleaning, filter changes and additional maintenance.
- Remanufacturing – by remanufacturing your old bearings instead of buying new ones, you can shorten the lead time to build spare segments. We can also add a new surface layer to your old rollers with laser cladding, significantly prolonging their service life.
Apart from remanufacturing your bearings, we can also remanufacture your rollers. For rollers, we can use laser metal deposition, which is less material-intensive and cools faster than traditional welding. With laser cladding, you can also add material to the roller all the way to the edge, and you need no additional heat treatment afterwards.