Balancing sustainability goals and cost
Bearings that fail without warning can cause costly downtime.
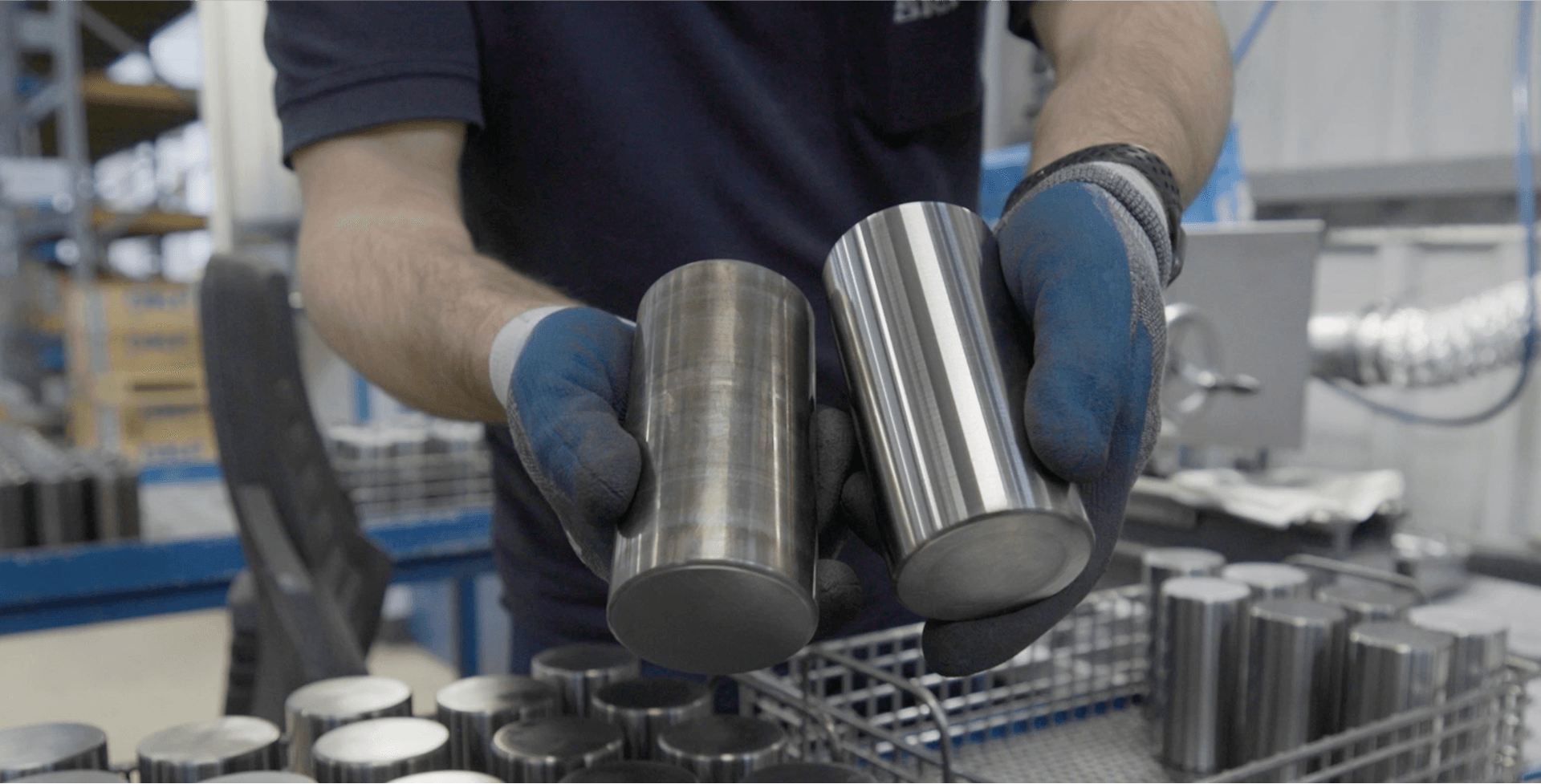
#9
Save money while reducing CO₂ emissions
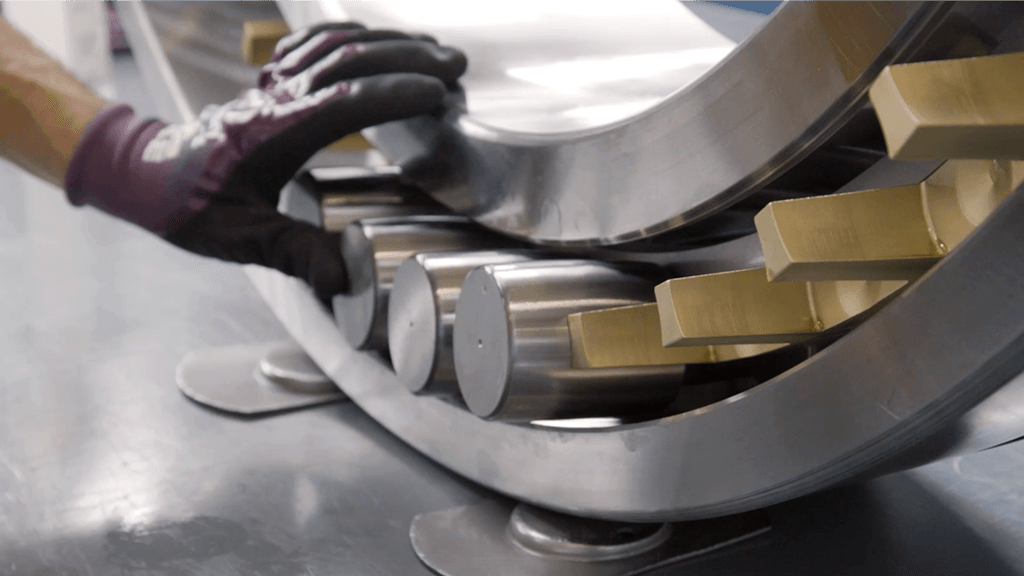
Ambitious sustainability goals and high expectations of profitability. Demands on reducing both CO₂ and costs at the same time. Balancing acts that many maintenance and production managers struggle with. However, the struggle can be solved – by not handling the different demands as conflicting targets. With SKF Remanufacturing, you can get the decarbonisation you need and save money simultaneously.
Remanufacturing solves it
Bearings installed in steel plant equipment, like continuous casters and rolling mills, can commonly be remanufactured between three and six times. This means a cost reduction of up to 50% compared to new bearings and an emission reduction of up to 90% every time you remanufacture a bearing. How? Because the remanufacturing process is less energy-intensive and requires fewer process steps and less new material than producing new bearings.
Calculate your estimate CO₂ savings by remanufacturing your bearings
CO₂ savings (kg) for total amount of bearings
-1.00kg CO₂
Want to learn more about what this result means for your specific business?
Contact meResults are based on the most common remanufacturing service level for continuous casting machines. Indicative avoided CO₂ emissions are estimates based on the avoided energy use in SKF's and SKF's suppliers production phases. The calculations are based on SKF Group global average data for 2021. Contact us if you require a more detailed calculation for your products.It has already been done
One of our customers, a large European steel company, cuts 30 tonnes of CO₂ yearly using remanufactured bearings in the slab caster machine. At the same time, they cut both costs and delivery times.
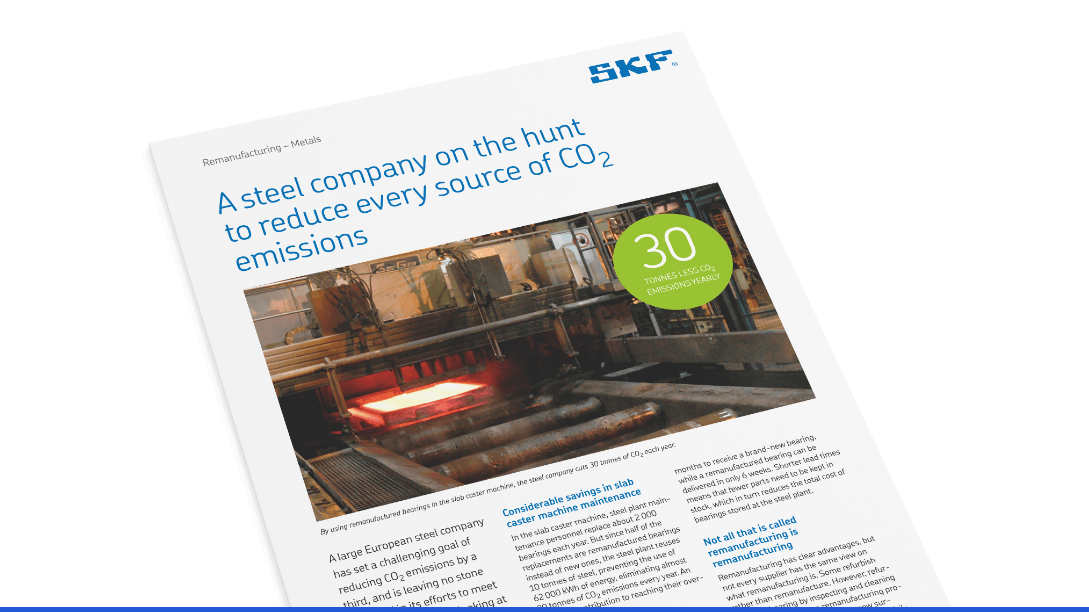