The high costs of replacing large bearings
To keep maintenance budgets low, many customers look for alternatives to replacing used bearings with brand-new ones.
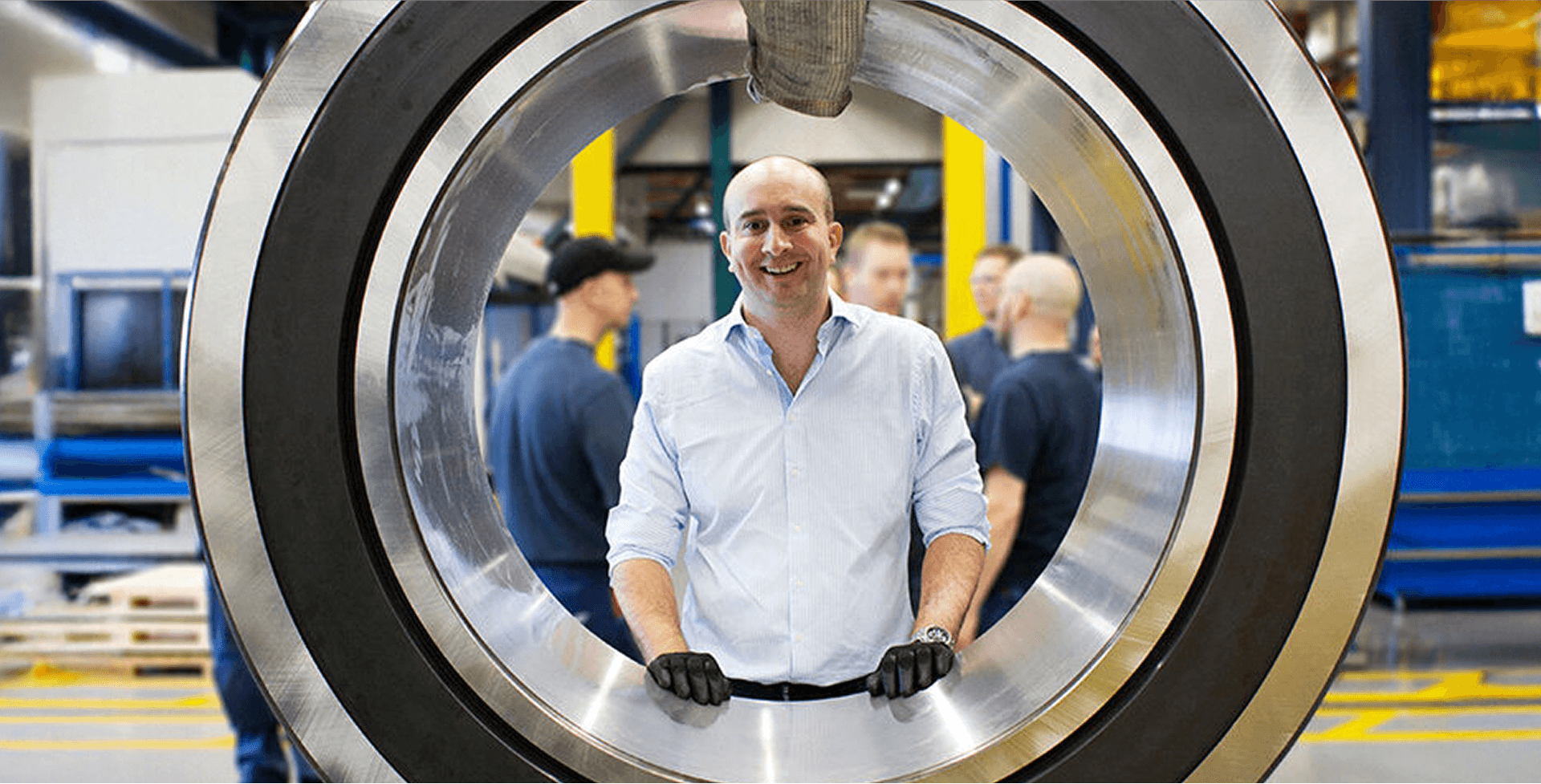
#5
Unlock the full potential of your bearings with remanufacturing
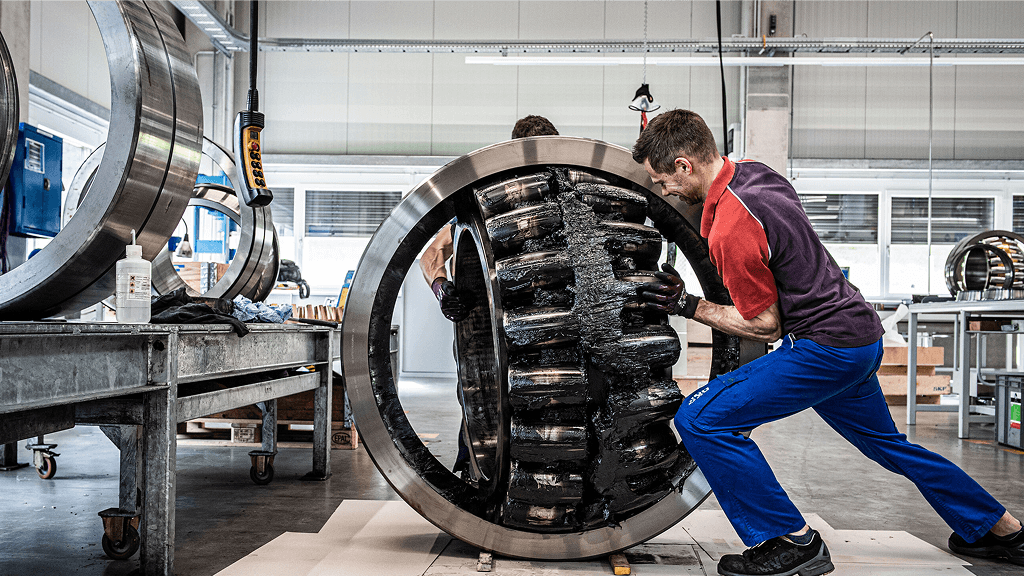
Many of the bearings installed in rolling mills can be remanufactured. This can sometimes be done twice, depending on their condition. Remanufacturing a bearing is one way to reduce costs, improve lead times, reduce CO₂ emissions, and significantly extend the bearings´ service life.
Extend service life
With SKF Remanufacturing, you can unlock the inherent potential of your bearings and extend their full useful life, while consuming fewer resources. Remanufacturing also enables a shorter delivery compared with ordering new bearings - and all this can be achieved while enjoying the same levels of SKF performance. You get reliable, remanufactured bearings according to SKF standards, documented CO₂ emissions reduction and an SKF warranty with the same conditions and duration as that for new bearings.
Keep costs and CO₂ down
The remanufacturing process is less energy-intensive and requires fewer process steps and less new material than producing new bearings. This delivers a cost reduction of up to 50% compared to new bearings and an emission reduction of up to 90% every time you remanufacture a bearing.
Remanufacturing: positive impact on service life
- Damage occurs
- First remanufacturing*
- Second remanufacturing*
- Potential service life without remanufacturing
- Potential service life after first remanufacturing
- Potential service life after second remanufacturing